I make front panels. This kind of thing -
The work i do is all mechanically cut (as in rotary engraved, rather than lasers, or metal photo etc) resulting in a professional, durable, finish.
The panels are then milled internally and externally. Up to 19" x 5u high is fairly standard for me, but i can do larger on request also.
Work can be infilled, eg -
Or left bare, eg -
All the metal i work with is anodised. Silver and matt black are the most common finishes, but i can do other colours, and even gloss finishes by arrangement. The unit above was cut in gloss black.
Common thicknesses are 1.5mm, 2.0mm, and 3.0mm.
My own personal interest is much more centred around synthesis of sound, rather than outboard kit, hence the i 'hang out' much more on those types of forums (muffwiggler, midibox, electro-music etc), and that's why most of my example work is modular stuff and the like.
I am based in the United Kingdom, however, historically, about 70% of my work has been export - so im quite happy to ship overseas.
I work from DXF, but there's a pathway to DXF from most common applications.
Thank you,
Julian
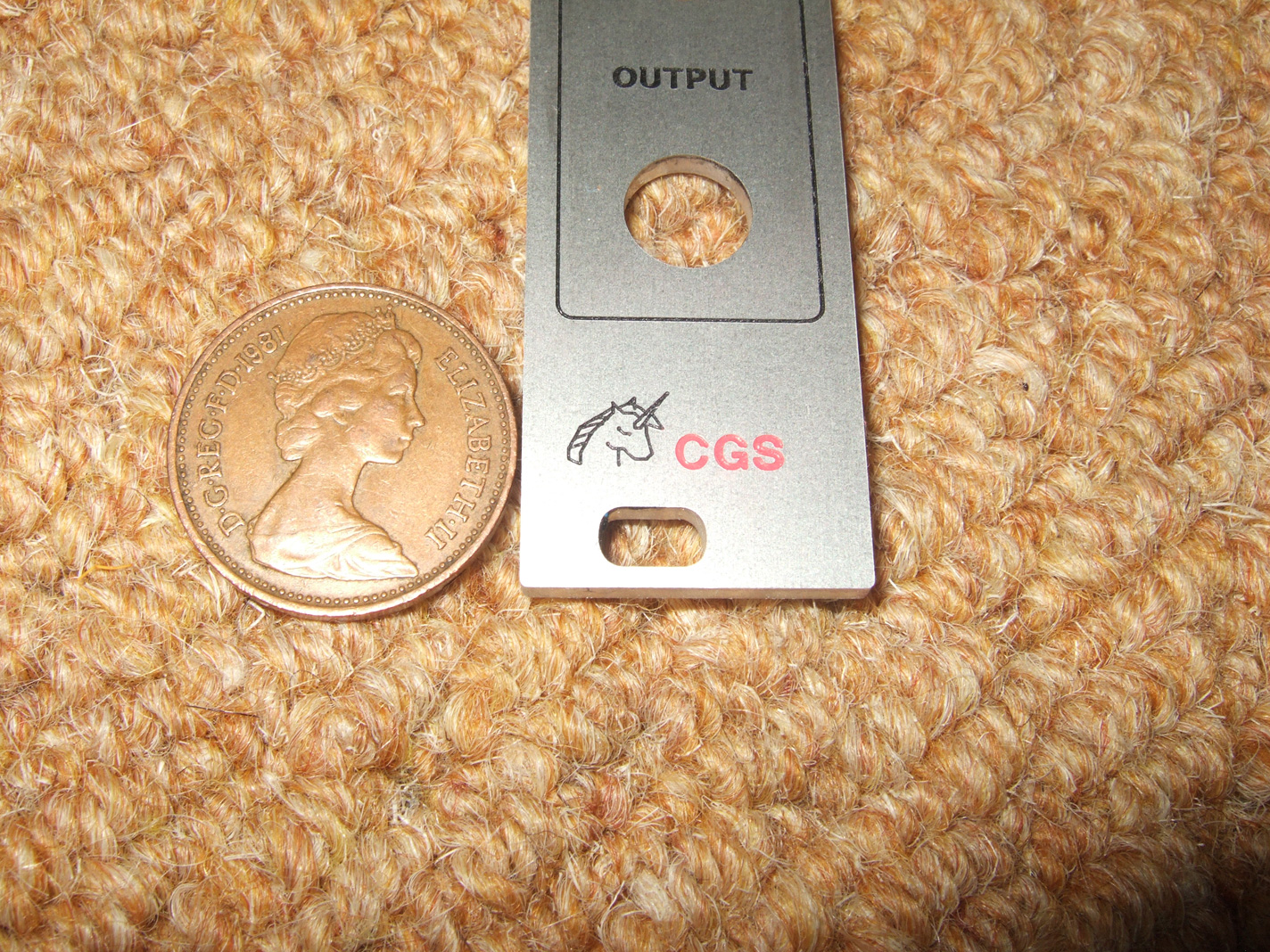
The work i do is all mechanically cut (as in rotary engraved, rather than lasers, or metal photo etc) resulting in a professional, durable, finish.
The panels are then milled internally and externally. Up to 19" x 5u high is fairly standard for me, but i can do larger on request also.
Work can be infilled, eg -
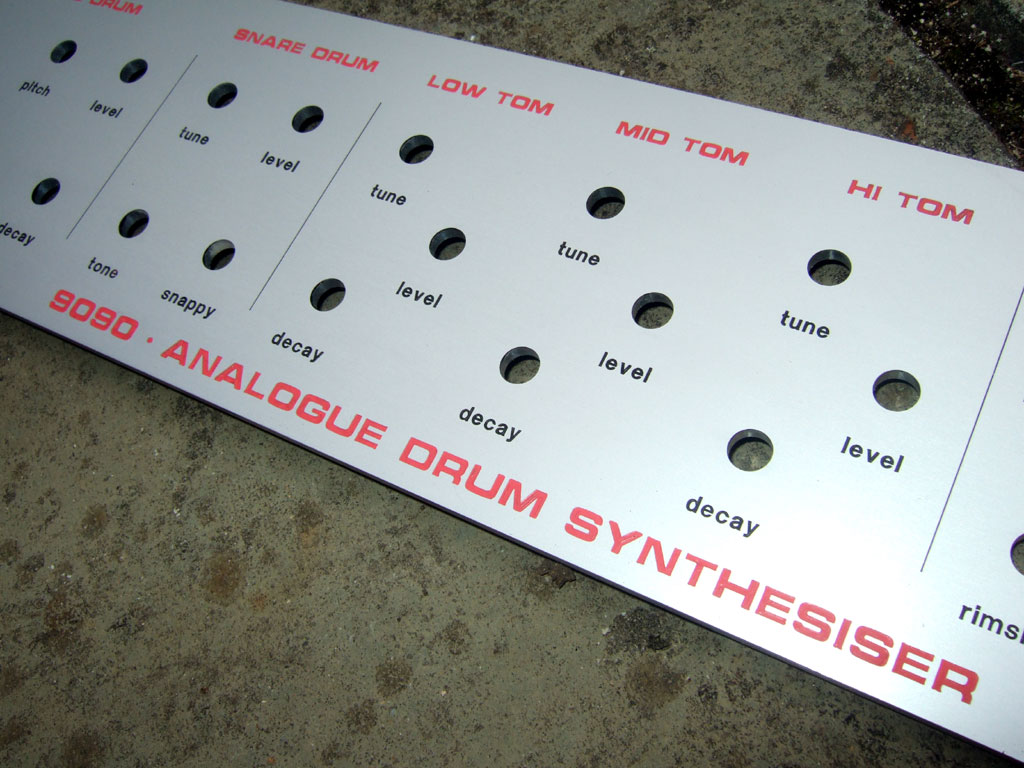
Or left bare, eg -
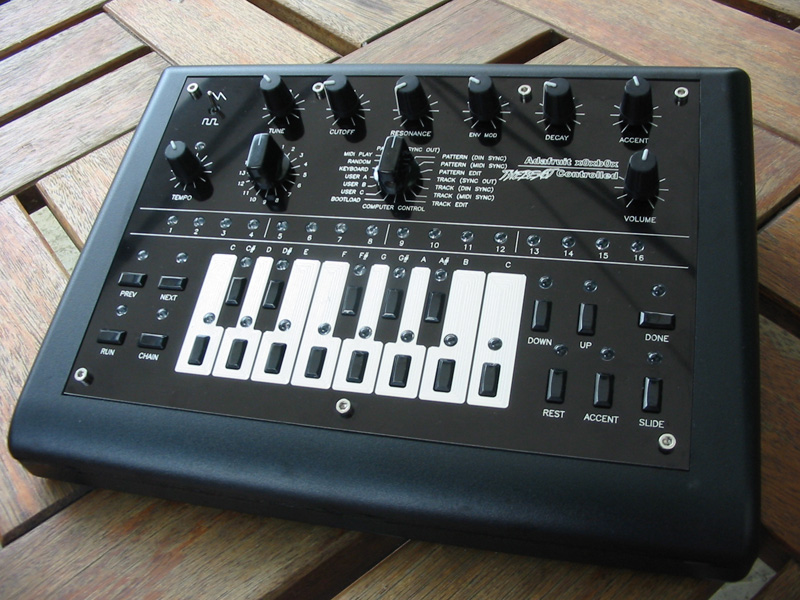
All the metal i work with is anodised. Silver and matt black are the most common finishes, but i can do other colours, and even gloss finishes by arrangement. The unit above was cut in gloss black.
Common thicknesses are 1.5mm, 2.0mm, and 3.0mm.
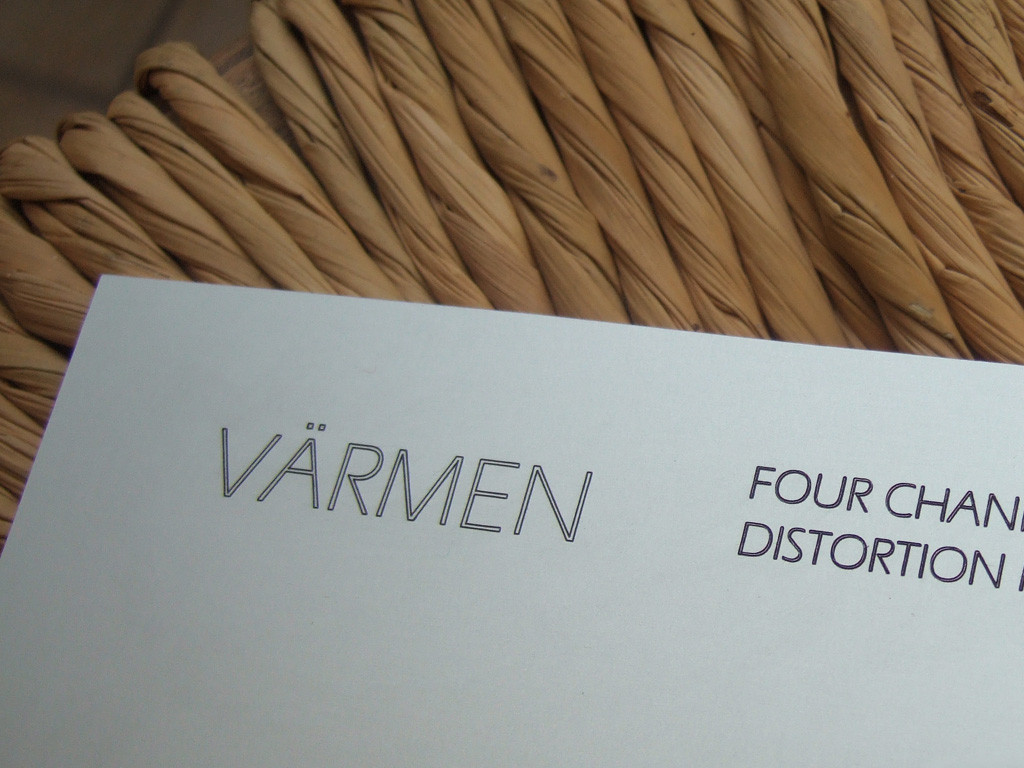
My own personal interest is much more centred around synthesis of sound, rather than outboard kit, hence the i 'hang out' much more on those types of forums (muffwiggler, midibox, electro-music etc), and that's why most of my example work is modular stuff and the like.
I am based in the United Kingdom, however, historically, about 70% of my work has been export - so im quite happy to ship overseas.
I work from DXF, but there's a pathway to DXF from most common applications.
Thank you,
Julian