Sometimes you get a multi-section cap capacitor that is mechanically integral to the construction of a piece. In this example, every connection relating to B+ feed is built off of the cap connections, and there's no room to build with new parts elsewhere. Maybe you could pull the original can, and find a little extra space, but then there'd be an obvious ugly hole in the chassis. Maybe, like this example, the original mounting wafer is riveted in place rather than screwed down.
Here's the solution, which also keeps original look intact.
Cut the can near the base, a hacksaw will do it in 20-30 seconds.
Drill through remaining cap base beside the original terminals, and once through the very center for the ground connection, only as large as needed for the new cap leads.
Run a drill into the core of the old cap, this will allow you to then pull out enough of the remaining layers of paper and foil to make room for new caps.
Tie the grounds of the new caps together as needed, insulate as needed.
Mount the new caps and solder the new leads to the original terminals on the circuit side.
Put the original can over the new caps, and heatshrink the can back to the base.
Here's the solution, which also keeps original look intact.
Cut the can near the base, a hacksaw will do it in 20-30 seconds.
Drill through remaining cap base beside the original terminals, and once through the very center for the ground connection, only as large as needed for the new cap leads.
Run a drill into the core of the old cap, this will allow you to then pull out enough of the remaining layers of paper and foil to make room for new caps.
Tie the grounds of the new caps together as needed, insulate as needed.
Mount the new caps and solder the new leads to the original terminals on the circuit side.
Put the original can over the new caps, and heatshrink the can back to the base.
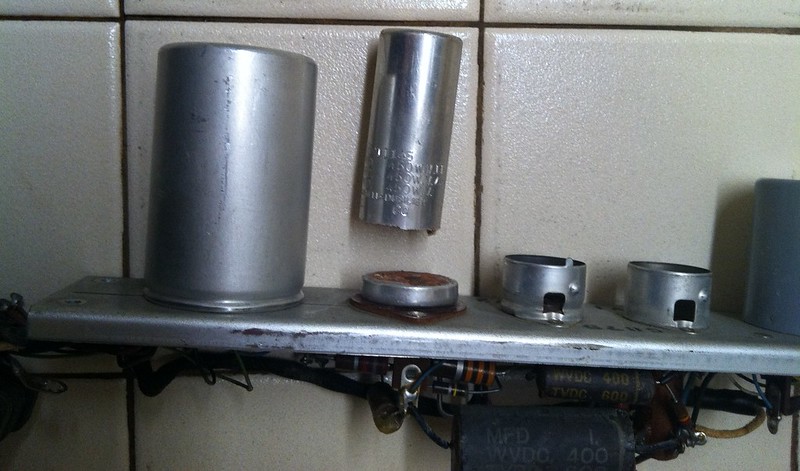
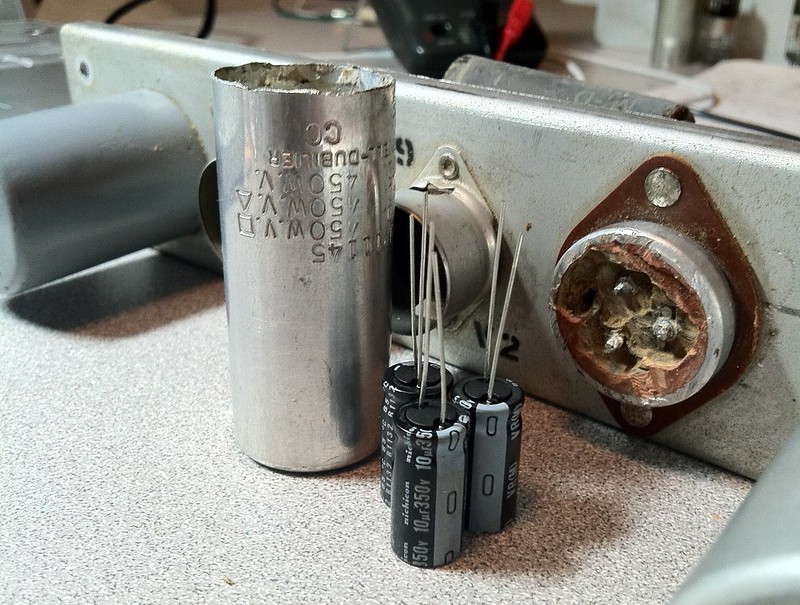
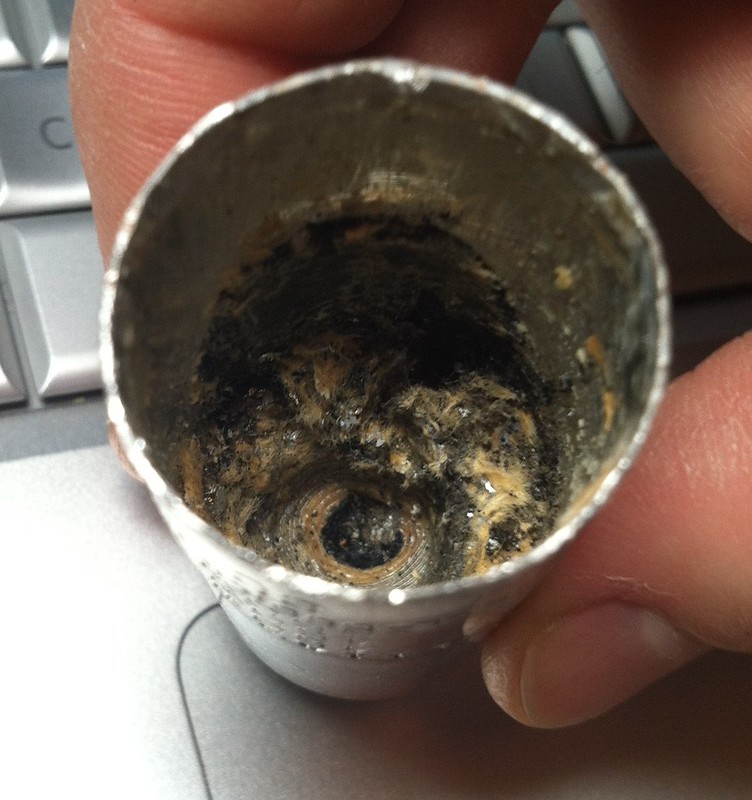
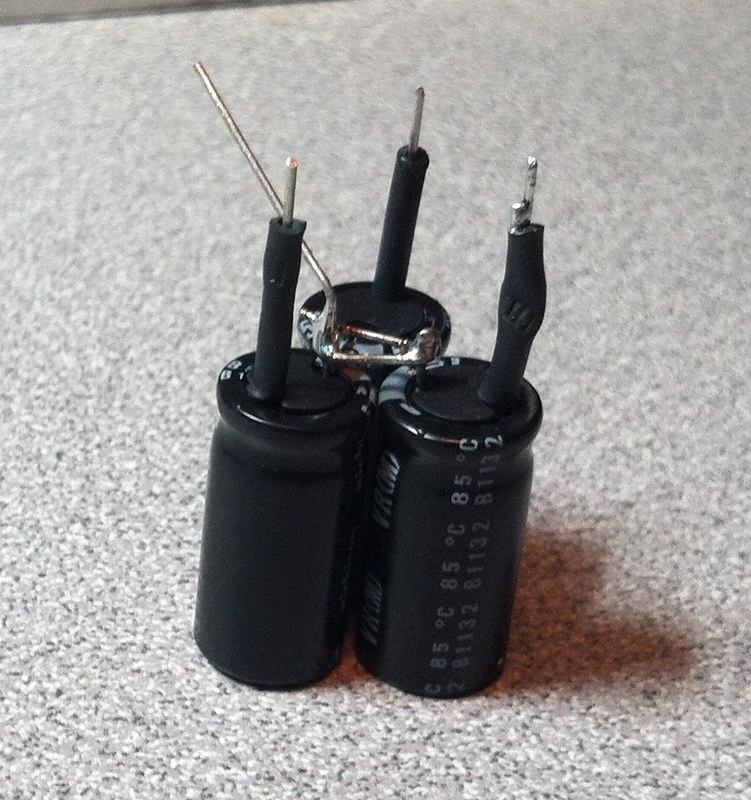
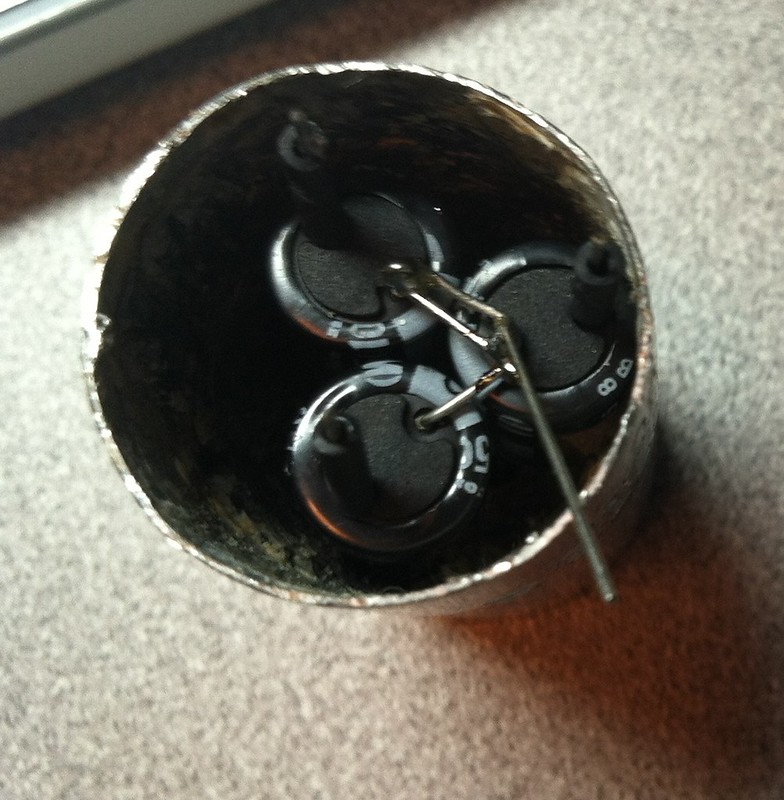
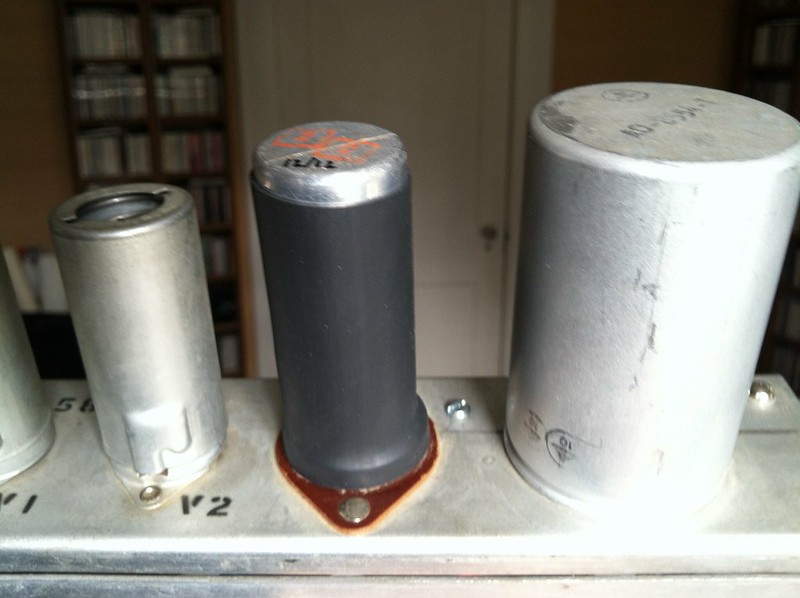
Last edited: