buildafriend
Well-known member
now I need to figure out a good plan. I figure I can fab a chassis in a few hours at the cost of sheet metal but what makes the most sense as a design? What is the best way to cut the sheet metal for cheap that leaves a clean edge? What metals are the best to use?
for those who don't know what youre looking at its a spot welder and a sheet metal break.
I could fab up chassis for really cheap for ya'll if this works out.
for those who don't know what youre looking at its a spot welder and a sheet metal break.
I could fab up chassis for really cheap for ya'll if this works out.
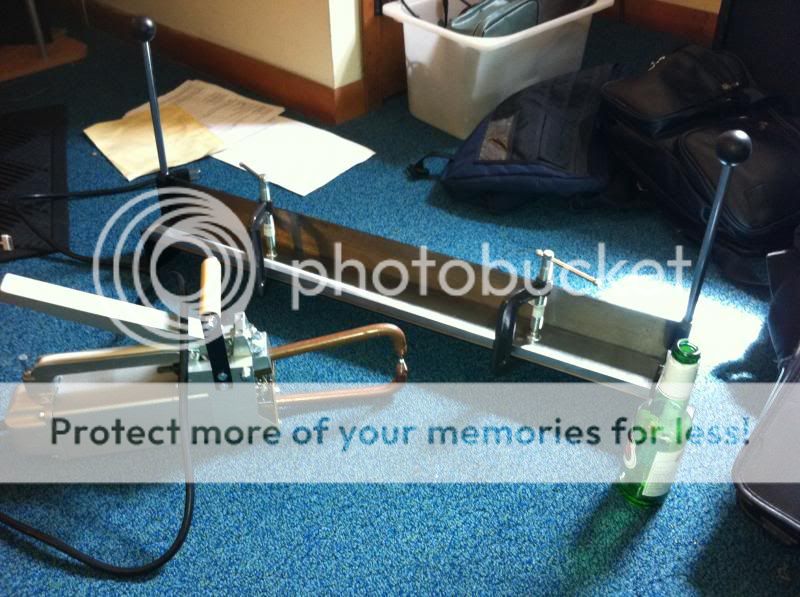