boji
Well-known member
Howdy,
Last night I ran across a simple toggle circuit from a Boss pedal that PRR shared some time ago. I can't seem to locate the thread today.
Might anyone know the one I'm talking about? I think uses two transistors instead of a cmos & Schmidt like the one below.
Additionally, I'm curious to know if you have a favorite circuit for switching with non-latching push buttons, and why. For my needs, it should pull a CV to ground to un-energize a separate dual relay circuit which includes debouncing.
Thank you!
Edit: I may try out the one below if the boss one can't be recalled:
Last night I ran across a simple toggle circuit from a Boss pedal that PRR shared some time ago. I can't seem to locate the thread today.
Might anyone know the one I'm talking about? I think uses two transistors instead of a cmos & Schmidt like the one below.
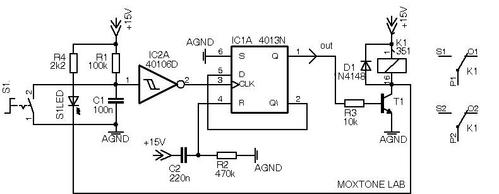
Additionally, I'm curious to know if you have a favorite circuit for switching with non-latching push buttons, and why. For my needs, it should pull a CV to ground to un-energize a separate dual relay circuit which includes debouncing.
Thank you!
Edit: I may try out the one below if the boss one can't be recalled:
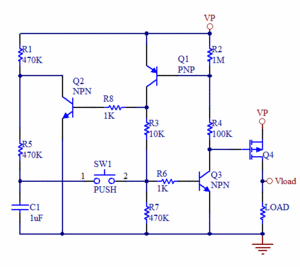