***ATTENTION!! The stepped VP312DI kits are now shipping with Grayhill switches that have factory set stops. This means there will be no stop-pins or stickers shipped or required. A quick glance at the switch should give this away as there are no holes to put the stop-pins in!!***
Hi everyone,
Since I don’t plan on an official assembly guide, this thread is to support my VP312DI project. Kits can be found here at capi-gear.com. This is a very unique preamp with the most versatile Direct Inject on the DIY or pro market, AFAIK. Many thanks to my friend Volker Mayer, [silent:arts], for the collaboration on the cool and fun HiZ Plug-In part of this project. We both hope to see the open format being used in other projects soon.
The VP312DI is pretty easy over all. It is a little more complicated than my other VP2x or VP312 builds. If you have built one of those, this should be no problem.
--------------------------------------------------------------------------------------------------------
September 21st, 2015 Update:
All support docs for this project can be found on the recently added Support Docs page at www.capi-gear.com
--------------------------------------------------------------------------------------------------------
--------------------------------------------------------------------------------------------------------
February 2nd, 2016 Update:
Rev D boards are now shipping for the VP312DI. To easily identify, the Rev D boards are green. The circuit is 100% identical although a few part labels and designations have changed. Like with all projects, it is crucially imperative that you follow the BOM that matches the revision of the PCB that you are building. I still have a good amount of the Sub DI boards left in black. Once those are gone, the reorder will be green and have the CAPI® affixed
--------------------------------------------------------------------------------------------------------
MAKE SURE YOU INSTALL ALL 12 MILL-MAX DOA SOCKETS FROM THE BOTTOM, LIKE I SHOW IN THE VP2x GUIDE. This is very important for the HiZ Plug-In, especially if you plan to use the Jensen tranny Plug-In.
-------------------------------------------------
1. Start With The T-Pad
(Rev B.1 only)
-------------------------------------------------
I start with the t-pad on the VP312DI build. I do this so I can use 2 of the small PCB’s as spacers between the body of the t-pad and the board. Other parts on the PCB at this time can get in the way. The desired space is 1/16”.
I have chosen to continue using the solder-lug version so Hairball Mike and I can combine our orders to help keep the prices down.
Solder only the 2 middle lugs at this time making sure that the t-pad is parallel to the PCB. This will allow for adjustment if needed.
Temporarily assembly the PCB to the L-Bracket. After securing the nuts, make sure the t-pad’s bushing and lug is centered in their respective openings.
Disassemble the PCB. Make any adjustments if necessary. When soldering the rest of the lugs, try not to over-heat the pot. A good, solid solder joint can be completed without filling the thru holes with solder.
-------------------------------------------------
2. The Bourns 25K potentiometer is next
(Any Rev)
-------------------------------------------------
Install the Bourns pot following the same general steps that can be found in the VP2x Assembly Guide. This will help to make sure the faceplate is aligned properly for the next few steps.
As a tip, you can temporarily attached the faceplate to the bracket with a Quick-Grip clamp. Make sure you center it over the bracket holes and keep it nice and even.
I mention the caps in that last pic as I change up my steps a little and combine some of the steps. I have built so many of these that I do little things to save time.
-------------------------------------------------
3. The Sub-DI.1 PCB Is Next
(Any Rev)
-------------------------------------------------
The next step is to fully populate the Sub-DI.1 board, with the exception of the 3 sub-mini switches.
Fit the Sub-DI.1 PCB on top of the main PCB, lining up the appropriate thru holes. I start with the 3 corner holes. For these 3, I use cut off leads from the Elna cap. They are the largest diameter leads in the kit. Slightly bend them and drop all 3 into the corner holes. This will lock the small board in and allow very little if any, movement.
Before soldering these 3 leads, I carefully clamp the 2 boards together.
It is very important that the 2 PCB’s are tight to each other. I check this before and after soldering the 3 leads from the top and the bottom.
I use cut off leads from the 1N4004 diodes for the remaining 5 holes. Again, a slight bend is all that is needed to keep them from falling thru.
-------------------------------------------------
4. The NKK Sub-Miniature Switches
(Any Rev)
-------------------------------------------------
Next we will fit all 3 of the NKK sub-mini switches to the bottom of the Sub-DI.1 PCB. Hold the switch bodies flat and tight to the board soldering only 1 of their bracket pins at this time.
Temporarily assembly the PCB, L-bracket and faceplate. Thumb tighten the 2 pot nuts making sure the faceplate alignment is nice and parallel to the L-bracket. The 3 mini toggles should fit nicely in their respective holes.
Turn the assembly over. You will have access to switch pins.
Carefully solder at least 2 additional pins for each of the switches. Try not to burn or melt any of the components!
Disassemble the PCB from the metal and finish soldering the switches.
***Clip the 3 pins for SW1. This needs to be done to make sure that they don’t later interfere with the Sub-DI.2 PCB.
-------------------------------------------------
5. Onto The Sub-DI.2 PCB
(Any Rev)
-------------------------------------------------
Fit the 4-pin 90° header to the Sub-DI.2 PCB. I like to clamp it to the board and solder from the bottom.
Next, fit the 1/4" Neutrik jack onto the PCB. It will snugly snap into place. Before soldering, you need to make sure that the edge of the jack housing sits slightly beyond the edge of the PCB. If the PCB is flush or proud of the jack housing, you should file or sand this edge of the Sub-DI.2 PCB.
I have randomly check a dozen or so of the boards and so far, have not found any that stick past. Making sure will just let the jack pull the PCB perpendicular to the faceplate for a neater looking assembly.
When you have confirmed the proper fit, solder the jack to the PCB.
Insert the 4-pin 90° header pins into the Sub-DI.1 PCB. DO NOT SOLDER at this time! Again, we will temporarily assemble the metalwork to the PCB assembly. Center the Neutrik jack in its faceplate hole. Put on the plastic washer and hand-snug the knurled nut.
After flipping the entire assembly over, you will have just enough access to solder all 4 pins of the 90° header.
-------------------------------------------------
Next you can take the assembly apart and complete the rest of the build as normal.
The remainder is pretty straight forward.
-------------------------------------------------
6a. Phantom LED
(Rev C.1 only)
-------------------------------------------------
The LED installation has changed a little for Rev C.1. A lot of the info in 6b is still pertinent so definitely go thru it. The end result should look more like this pic though.
-------------------------------------------------
6b. Phantom LED
(Rev B.1 only)
-------------------------------------------------
For me, the last step before the knob and bullet cap dressing is the phantom LED. I solder 2 small transformer lead cut-offs to the pads labeled 1 and 2. Those will be routed to the C&K toggle as shown.
I prep the LED by cutting a piece of shrink tubing a little less than 1”. Slip it onto the shorter or cathode lead. I bend about a 1/16” L onto the end of this lead.
Insert the LED into the hole in the faceplate keeping the longer anode lead to the left and the shorter cathode lead to the right. Slightly bend the cathode lead down and solder it to the last lug on the Mute switch.
Next, insert 1 lead from a 10K resistor and the lead from solder pad 2 into the middle lug of the C&K toggle switch. I adjust the anode lead of the LED and the other lead of the 10K R so they touch. Solder and trim the leads back.
There are probably a number of different ways to do this so modify as you see fit.
BTW, the drop over the 10K R is about .21 watts. I have not had any problems with a 10K 1/4 watt resistor here. If you want the LED brighter and change the R to anything less than 10K, I would recommend using a 1/2 watt R.
Here’s another angle. Note that if you thread the nut on the C&K toggle first, then the lock washer, then into the metal, the larger trim nut will fit nicely on the front side.
Have fun!!
Cheers, Jeff
Hi everyone,
Since I don’t plan on an official assembly guide, this thread is to support my VP312DI project. Kits can be found here at capi-gear.com. This is a very unique preamp with the most versatile Direct Inject on the DIY or pro market, AFAIK. Many thanks to my friend Volker Mayer, [silent:arts], for the collaboration on the cool and fun HiZ Plug-In part of this project. We both hope to see the open format being used in other projects soon.
The VP312DI is pretty easy over all. It is a little more complicated than my other VP2x or VP312 builds. If you have built one of those, this should be no problem.
--------------------------------------------------------------------------------------------------------
September 21st, 2015 Update:
All support docs for this project can be found on the recently added Support Docs page at www.capi-gear.com
--------------------------------------------------------------------------------------------------------
--------------------------------------------------------------------------------------------------------
February 2nd, 2016 Update:
Rev D boards are now shipping for the VP312DI. To easily identify, the Rev D boards are green. The circuit is 100% identical although a few part labels and designations have changed. Like with all projects, it is crucially imperative that you follow the BOM that matches the revision of the PCB that you are building. I still have a good amount of the Sub DI boards left in black. Once those are gone, the reorder will be green and have the CAPI® affixed
--------------------------------------------------------------------------------------------------------
MAKE SURE YOU INSTALL ALL 12 MILL-MAX DOA SOCKETS FROM THE BOTTOM, LIKE I SHOW IN THE VP2x GUIDE. This is very important for the HiZ Plug-In, especially if you plan to use the Jensen tranny Plug-In.
-------------------------------------------------
1. Start With The T-Pad
(Rev B.1 only)
-------------------------------------------------
I start with the t-pad on the VP312DI build. I do this so I can use 2 of the small PCB’s as spacers between the body of the t-pad and the board. Other parts on the PCB at this time can get in the way. The desired space is 1/16”.
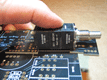
I have chosen to continue using the solder-lug version so Hairball Mike and I can combine our orders to help keep the prices down.
Solder only the 2 middle lugs at this time making sure that the t-pad is parallel to the PCB. This will allow for adjustment if needed.
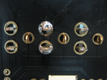
Temporarily assembly the PCB to the L-Bracket. After securing the nuts, make sure the t-pad’s bushing and lug is centered in their respective openings.
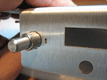
Disassemble the PCB. Make any adjustments if necessary. When soldering the rest of the lugs, try not to over-heat the pot. A good, solid solder joint can be completed without filling the thru holes with solder.
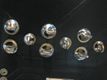
-------------------------------------------------
2. The Bourns 25K potentiometer is next
(Any Rev)
-------------------------------------------------
Install the Bourns pot following the same general steps that can be found in the VP2x Assembly Guide. This will help to make sure the faceplate is aligned properly for the next few steps.
As a tip, you can temporarily attached the faceplate to the bracket with a Quick-Grip clamp. Make sure you center it over the bracket holes and keep it nice and even.
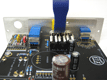
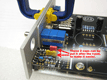
I mention the caps in that last pic as I change up my steps a little and combine some of the steps. I have built so many of these that I do little things to save time.
-------------------------------------------------
3. The Sub-DI.1 PCB Is Next
(Any Rev)
-------------------------------------------------
The next step is to fully populate the Sub-DI.1 board, with the exception of the 3 sub-mini switches.
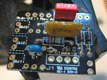
Fit the Sub-DI.1 PCB on top of the main PCB, lining up the appropriate thru holes. I start with the 3 corner holes. For these 3, I use cut off leads from the Elna cap. They are the largest diameter leads in the kit. Slightly bend them and drop all 3 into the corner holes. This will lock the small board in and allow very little if any, movement.
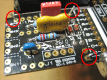
Before soldering these 3 leads, I carefully clamp the 2 boards together.
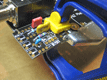
It is very important that the 2 PCB’s are tight to each other. I check this before and after soldering the 3 leads from the top and the bottom.
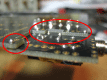
I use cut off leads from the 1N4004 diodes for the remaining 5 holes. Again, a slight bend is all that is needed to keep them from falling thru.
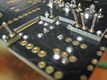
-------------------------------------------------
4. The NKK Sub-Miniature Switches
(Any Rev)
-------------------------------------------------
Next we will fit all 3 of the NKK sub-mini switches to the bottom of the Sub-DI.1 PCB. Hold the switch bodies flat and tight to the board soldering only 1 of their bracket pins at this time.
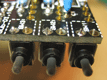
Temporarily assembly the PCB, L-bracket and faceplate. Thumb tighten the 2 pot nuts making sure the faceplate alignment is nice and parallel to the L-bracket. The 3 mini toggles should fit nicely in their respective holes.
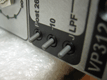
Turn the assembly over. You will have access to switch pins.
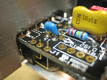
Carefully solder at least 2 additional pins for each of the switches. Try not to burn or melt any of the components!
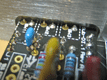
Disassemble the PCB from the metal and finish soldering the switches.
***Clip the 3 pins for SW1. This needs to be done to make sure that they don’t later interfere with the Sub-DI.2 PCB.
-------------------------------------------------
5. Onto The Sub-DI.2 PCB
(Any Rev)
-------------------------------------------------
Fit the 4-pin 90° header to the Sub-DI.2 PCB. I like to clamp it to the board and solder from the bottom.
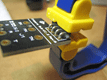
Next, fit the 1/4" Neutrik jack onto the PCB. It will snugly snap into place. Before soldering, you need to make sure that the edge of the jack housing sits slightly beyond the edge of the PCB. If the PCB is flush or proud of the jack housing, you should file or sand this edge of the Sub-DI.2 PCB.
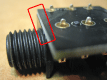
I have randomly check a dozen or so of the boards and so far, have not found any that stick past. Making sure will just let the jack pull the PCB perpendicular to the faceplate for a neater looking assembly.
When you have confirmed the proper fit, solder the jack to the PCB.
Insert the 4-pin 90° header pins into the Sub-DI.1 PCB. DO NOT SOLDER at this time! Again, we will temporarily assemble the metalwork to the PCB assembly. Center the Neutrik jack in its faceplate hole. Put on the plastic washer and hand-snug the knurled nut.
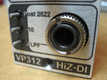
After flipping the entire assembly over, you will have just enough access to solder all 4 pins of the 90° header.
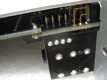
-------------------------------------------------
Next you can take the assembly apart and complete the rest of the build as normal.
The remainder is pretty straight forward.
-------------------------------------------------
6a. Phantom LED
(Rev C.1 only)
-------------------------------------------------
The LED installation has changed a little for Rev C.1. A lot of the info in 6b is still pertinent so definitely go thru it. The end result should look more like this pic though.
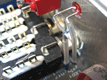
-------------------------------------------------
6b. Phantom LED
(Rev B.1 only)
-------------------------------------------------
For me, the last step before the knob and bullet cap dressing is the phantom LED. I solder 2 small transformer lead cut-offs to the pads labeled 1 and 2. Those will be routed to the C&K toggle as shown.
I prep the LED by cutting a piece of shrink tubing a little less than 1”. Slip it onto the shorter or cathode lead. I bend about a 1/16” L onto the end of this lead.
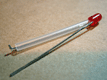
Insert the LED into the hole in the faceplate keeping the longer anode lead to the left and the shorter cathode lead to the right. Slightly bend the cathode lead down and solder it to the last lug on the Mute switch.
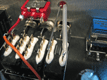
Next, insert 1 lead from a 10K resistor and the lead from solder pad 2 into the middle lug of the C&K toggle switch. I adjust the anode lead of the LED and the other lead of the 10K R so they touch. Solder and trim the leads back.
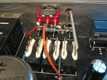
There are probably a number of different ways to do this so modify as you see fit.
BTW, the drop over the 10K R is about .21 watts. I have not had any problems with a 10K 1/4 watt resistor here. If you want the LED brighter and change the R to anything less than 10K, I would recommend using a 1/2 watt R.
Here’s another angle. Note that if you thread the nut on the C&K toggle first, then the lock washer, then into the metal, the larger trim nut will fit nicely on the front side.
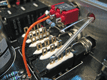
Have fun!!
Cheers, Jeff