Ok, so I've been reading through the datasheet a bit, here's rev 2.
Had to go up on the transformer size from the datasheet, but the Wurth transformer (PN 750310349) seems perfect for the job (near as I can tell). Not sure if this method of using inductors to isolate the "clean" 12V for heaters from the "dirty" 12V for the flyback transformer will work - open to feedback there.
Other values like RFB, Rsense, etc. have been selected to produce 250VDC out, and this should accommodate roughly 230 mA on the HT - which seems like more than plenty.
Maximum current should be 16A in the MOSFET / primary. The primary inductance of the transformer is 5 uH, while this requires a minimum of 4 uH - so "seems" ok.
Minimum load in the datasheet is ~2%, which in this case would be ~5 mA. You could add a zener to establish that load.
One thing I'm not sure about is the jumper between pins 1 and 5 on the LT3748. This is the INTVcc pin, and the datasheet says it "may" be connected if no third winding is used and Vin < 20V. I don't know whether "may" means "should"?
Thoughts? Comments? Complaints? ;D
Had to go up on the transformer size from the datasheet, but the Wurth transformer (PN 750310349) seems perfect for the job (near as I can tell). Not sure if this method of using inductors to isolate the "clean" 12V for heaters from the "dirty" 12V for the flyback transformer will work - open to feedback there.
Other values like RFB, Rsense, etc. have been selected to produce 250VDC out, and this should accommodate roughly 230 mA on the HT - which seems like more than plenty.
Maximum current should be 16A in the MOSFET / primary. The primary inductance of the transformer is 5 uH, while this requires a minimum of 4 uH - so "seems" ok.
Minimum load in the datasheet is ~2%, which in this case would be ~5 mA. You could add a zener to establish that load.
One thing I'm not sure about is the jumper between pins 1 and 5 on the LT3748. This is the INTVcc pin, and the datasheet says it "may" be connected if no third winding is used and Vin < 20V. I don't know whether "may" means "should"?
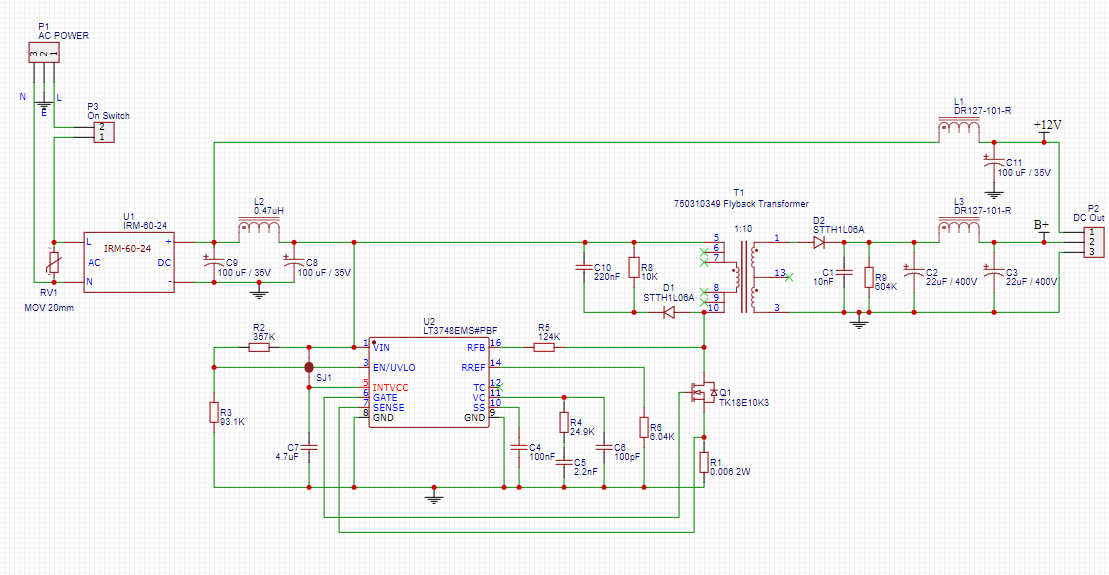
Thoughts? Comments? Complaints? ;D