nedonnelly
Member
- Joined
- Jun 28, 2017
- Messages
- 18
So I'm kind of at a head-scratching place on my project. I've gotten all of my xlr's through, but I am having the hardest time figuring out how to line the holes for the screws up exactly in the right place. I've tried rubber cementing the xlr's to the panel, but that didn't work as the xlrs weren't sticking. I tried tracing the xlrs while in the PCB, but that didn't work as it still doesn't line up well. So I am here to ask for help. Any suggestions from those who have done this before?
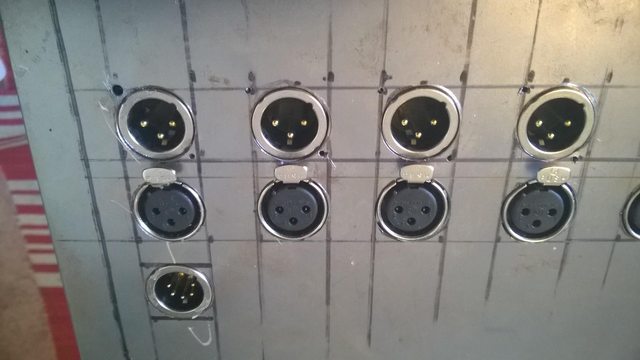